Bench Testing An Alternator
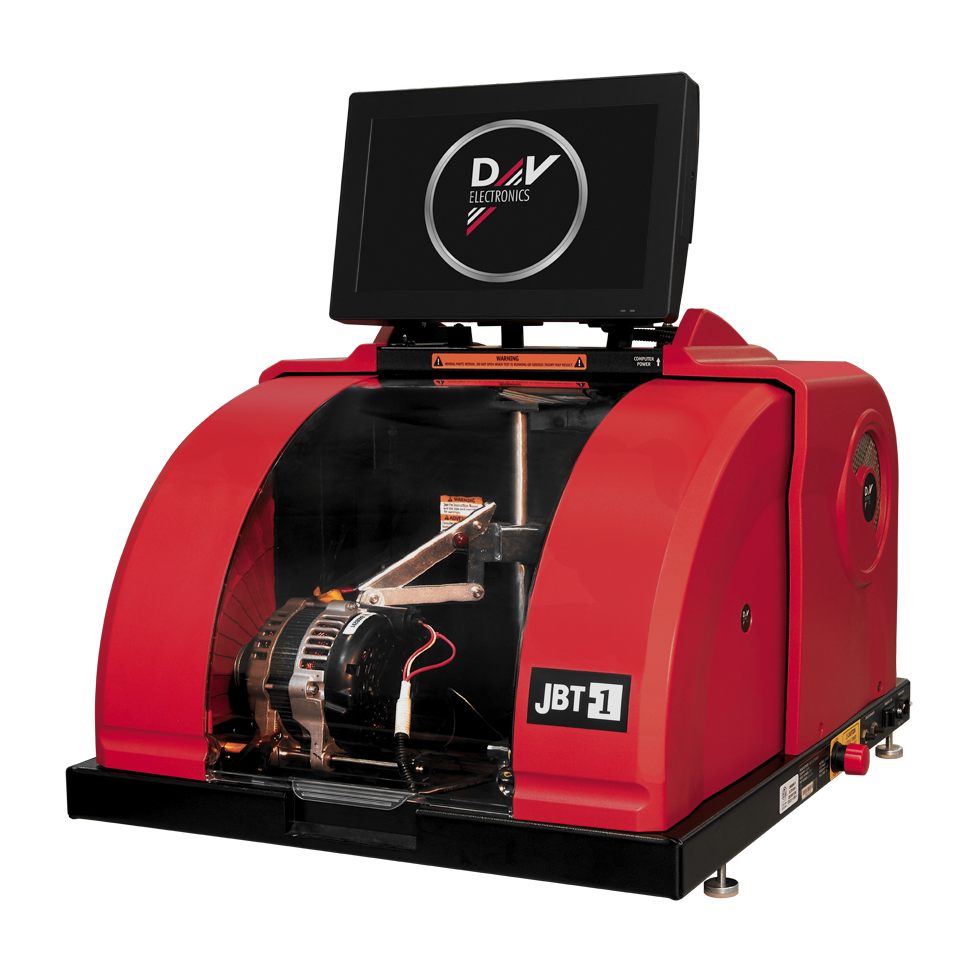
On a typical engine your alternator is usually driven at about 3 times the engine speed.
Bench testing an alternator. If it s below that charge the battery with a battery charger before you conduct the test again. With the engine off battery voltage should be between 12 5 and 12 8 volts. If the unit tests bad your customer needs a replacement alternator.
Get a cheap voltmeter. You should check if its connector is well plugged in if its fuse is right and if it is really working check alternator belt. If the old alternator passes the tests the problem is obviously not the alternator and you ve missed something.
Then start the engine and check for increased voltage readings. Or at least that used to be a common drive ratio so if you are assuming a 1500 rpm engine speed you need to spin that alternator about 3500 rpm. Conduct a voltmeter test.
Part 1 testing the alternator voltage output with the multimeter in volts dc mode. Part 3 verifying that the alternator fuse in the fuse box is not blown if equipped. Bench testing an alternator on a test stand should verify whether or not its output is within specifications.
Alternator is an electrical generator which uses engine power to turn a belt to charge the battery. Check the reading on the voltmeter again. You could check cabling as well.
Another approach for reducing comebacks and unnecessary warranty returns is to ask your parts supplier to bench test your customer s old alternator and to bench test the new alternator before you install it. If you see higher readings chances are the alternator is good. Batteries are charged when engine is running thanks to a device called alternator.